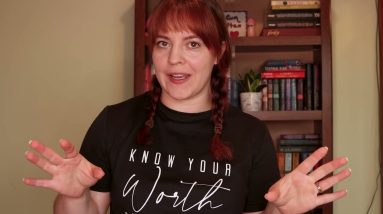
Sex Toy Review – Marco Napoli Porn Star Lifecast Realistic Silicone Dildo from Mr. Hankey’s Toys
The Best Robotic Blowjob Machine For Men A robotic blowjob machine is a sex toy that can do exactly what it says on the tin: suck your wiener horn like a real woman. They can be the perfect sex toy…
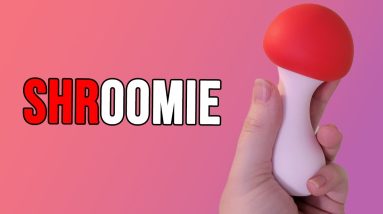
Sex Toy Review – Maia Toys Shroomie Rechargeable Silicone Mushroom Vibrator
Best Male Masturbator – A Robotic Blowjob Machine Robots are everywhere in this day and age – they’re automating production processes, driving cars, and even helping you find love through online dating. So it’s only natural that they’d start making…
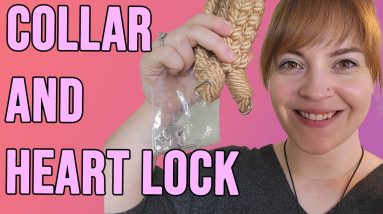
BDSM Review – Shibari Bondage Rope Collar and Heart Lock Pendant from Liebe Seele
Robotic BJ Machine – The Best Male Stroker This Year Robots have taken over many areas of our lives, including automated production processes, food distribution, and even online dating. So it’s only natural that somebody would figure out a way…
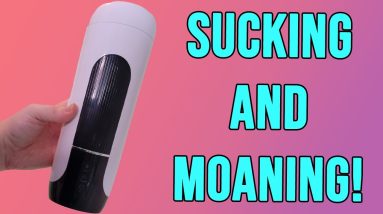
Sex Toy Review – Saith Wearable 7 Thrusting & Vibrating Heating Vocable Masturbation Cup
Best Male Robotic Blowjob Machine A robotic blowjob machine is a piece of technology that is engineered and built with great attention to detail. It is meant to mimic a woman’s mouth and vagina for an experience that is completely…
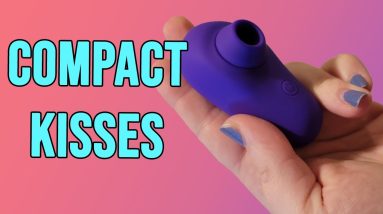
Sex Toy Review – Calexotics Neon Vibe Kissing Vibrator, Easy Grip Air Pulse Pleasure
Choosing the Best Male Stroker Robotic Blowjob Machine Fire, the bow and arrow, the internal combustion engine, transistors, the Internet — human history is replete with groundbreaking inventions and scientific insight, so it was only a matter of time before…
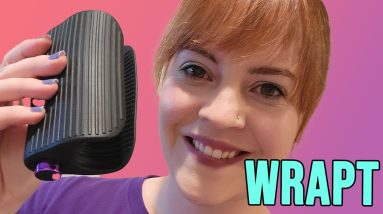
Sex Toy Review – M Elite Blush Platinum Silicone Wrapt Stroker and Vibrating Masturbator
A Robotic Blowjob Machine Will Give You Oral Sex Like a Human Whether you’re looking for an automatic blowjob machine or a masturbator that’s the next best thing to a real human being giving you oral sex, there are plenty…
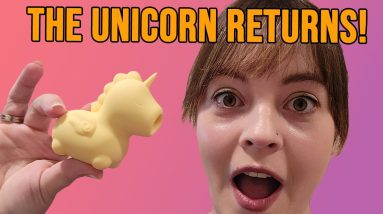
Sex Toy Review – Unihorn Unicorn Bean Blossom Clitoral Air Pulse and Tongue Vibrator with Two Motors
Robotic Blowjob Machine Robotic blowjob machine is a toy that mimics the feeling of oral sensations from another person. It works like a male stroker but instead of using your saliva to stroke your cock, it uses vibrators and vibrations…